Last updated: 30 Apr 2023
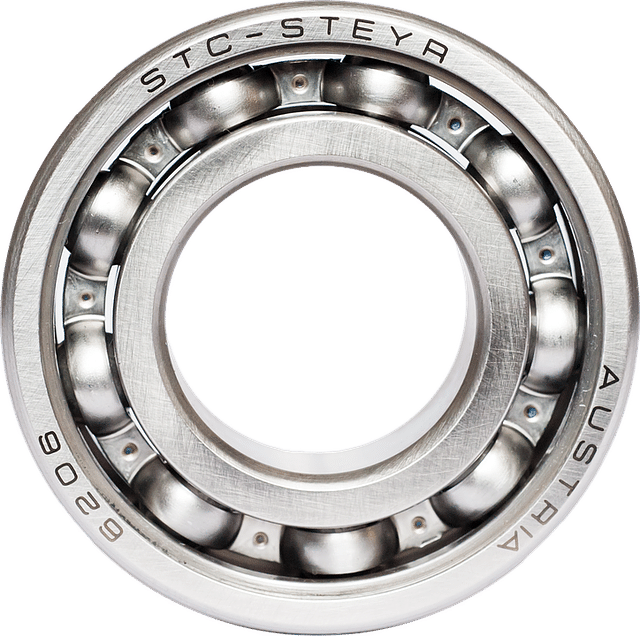
Greasing a sealed bearing is important because it helps to ensure that the bearing operates smoothly and efficiently, without any unnecessary friction or wear. The grease acts as a lubricant, helping to reduce the amount of heat generated by the bearing as it rotates. This in turn can help to prolong the life of the bearing, reducing the likelihood of premature failure and the need for costly repairs or replacements.
Proper lubrication can also help to reduce the amount of noise and vibration produced by the bearing, which can be important in applications where noise levels need to be kept to a minimum. Additionally, regular greasing can help to prevent contaminants from entering the bearing and causing damage, which can also help to prolong its lifespan.
Overall, greasing a sealed bearing is an important maintenance task that can help to ensure reliable performance, extend the lifespan of the bearing, and save money and time on repairs and replacements.
Roller bearings lubrication is amongst the most misinterpreted and misapplied duties in the business. Is it correct that 40 percent of the total bearings don’t ever reach the end of their designed life span, and that improper lubricating is the primary factor of this insubstantiality.
What you will need to follow this tutorial?
Prepare all of the required equipment for this DIY work before you begin to just save time and hassle:
- Hammer
- Slip joint pliers
- Degreaser solution
- Grease seals
- Needle-nose pliers
- Parts cleaning brush
- Marine wheel bearing grease
- Cotter pins
A seal remover, parts brush, washing tub, jack supports, floor jack, side cutters, and latex gloves will also be required.
Step by step instructions
Step 1: Take Out the Outer Bearing
Raise the trailer and use jack supports to hold the chassis or wheels. Using slip-joint tweezers, detach the wheel and afterward the hub dust cap. Untwist the yoke pin and use side scissors to pry the head out of its bridge nut.
Using forceps, twist the screw off. Move the hub forward until the outer bearing and washer come into your hands. Check out this video for more clarity
Step 2: Take Out the Inner Bearing
Remove the whole hub from the frame and set it on the ground. Grasp it in place with your shoe while using the seal remover to push away the oil sealing. Separate both the inner and outer bearing; they must be returned to their normal positions.
Step 3: Cleanup the Bearings
Immerse the bearing in the cleaner and scrub away all the previous dirt and grime with the tools brush. For drying, place them on a clean towel or use a compressor. However, never use pressurized air to twirl them; they’ll fly off and inflict catastrophic injury.
Look for symptoms of overheated deterioration, cutting, or cracking on the bearing sliders and courses. If any breakage is discovered, change the bearing and helix.
Step 4: Refill the grease
In your hand, smear a glob of fresh oil. Then smack the bearing’s tip into the grease. As though dumping dip with a French fry, push the oil into the bearings plate. Continue the cycle till the bearing box is filled with lubricant. Apply the remaining grease to the bearing rollers’ faces.
Step 5: Replace the grease seal
Remove the old lard from the hub. After that, re-grease the internal race and install the gear. Place the new grease protective coating on the bearing with the open rim of the lip facing in.
Bump a flat steel plate or wood frame into the spot over the seal until it has been fully perched. After that, apply a thin coat of oil to the interior of the new sealing.
Step 6: Reinstall the hub
Clean the wheel of any old grease. Place the hub, external bearing, gasket, and bridge nut on the shaft. Screw the bridge nut until it has been securely fastened. To distribute the grease and install the bearings, rotate the hub.
Return the bridge nut to its original position, and back it off a 1⁄4 turn to align it with the spindle hole. Bow the ears and install a new culvert key. Place the dirt cap on top.
Pro tips
- Always use right grease that is of good quality
- Apply a thin layer of grease to the wheel hub and bearing
- Allow at least 30 minutes for the grease to dry before using
- Using a cloth or your finger, rub the lubricant into the bearing and wheel hub
- Do not work on the bearings or wheel hubs if they are damp
- Don’t ever wash sealed bearings with a solvent
FAQs
How do you put grease on a sealed bearing?
Take a glob of bearing in your hand. Wearing rubber gloves is a good idea because it makes cleaning a lot simpler. Scrape tiny amounts of the glob of grease away with the other hand while holding the bearing.
Throughout the operation, keep turning the bearing to assist push the grease into the bearing. The grease will ultimately be pushed in the contrary direction. After it’s done, examine the bearing for any empty spots and apply a little coat of grease to the exterior of the bearing.
Should you lubricate a sealed bearing?
Usually, sealed bearings are pre-greased with a 25 percent to 35 percent grease load from the manufacturer. Since the relubrication period is greater than the bearing’s estimated life, that’s all the grease the bearings will ever require.
So don’t just believe what you see. It’s enticing to lubricate the bearings every day or to keep pumping until grease flows out from between the seals. Consequently, this, essentially kills the seal’s capacity to keep impurities out from the grease, and far too much grease “churns” inside the bearings, causing friction and fast heating.
Can you put too much grease in a bearing?
Excessive grease results in “churning”. Churning occurs when the bearing has to work way harder to move through the extra lubrication, causing the grease to deteriorate and perhaps scorch. Greasing a bearing till it is entirely loaded with grease may dramatically reduce its lifetime in most conditions.
What is the best bearing lubricant?
Although oil is used in some bearing applications, grease is the lubricant of preference for 80% to 90% of bearings. Grease sticks to bearing plates stronger than oil last a lot longer, and is less prone to flow off or be expelled from spinning parts.
Conclusion
So, what do you think of our tutorial? We’re certain that after reading this article, you’ll have a better grasp of how to grease a sealed bearing and why it’s so vital. Early bearing problems are a major source of productivity losses and wasteful expense. The majority of these incidents are caused by poor or irregular bearing service.
You may save a lot of money by using the above-mentioned method of lubricating the sealed bearing. If you have any questions, please leave a comment below. Also, if you like the content, please share it with others.
Related Reviews You Might Like:
Leave a Reply